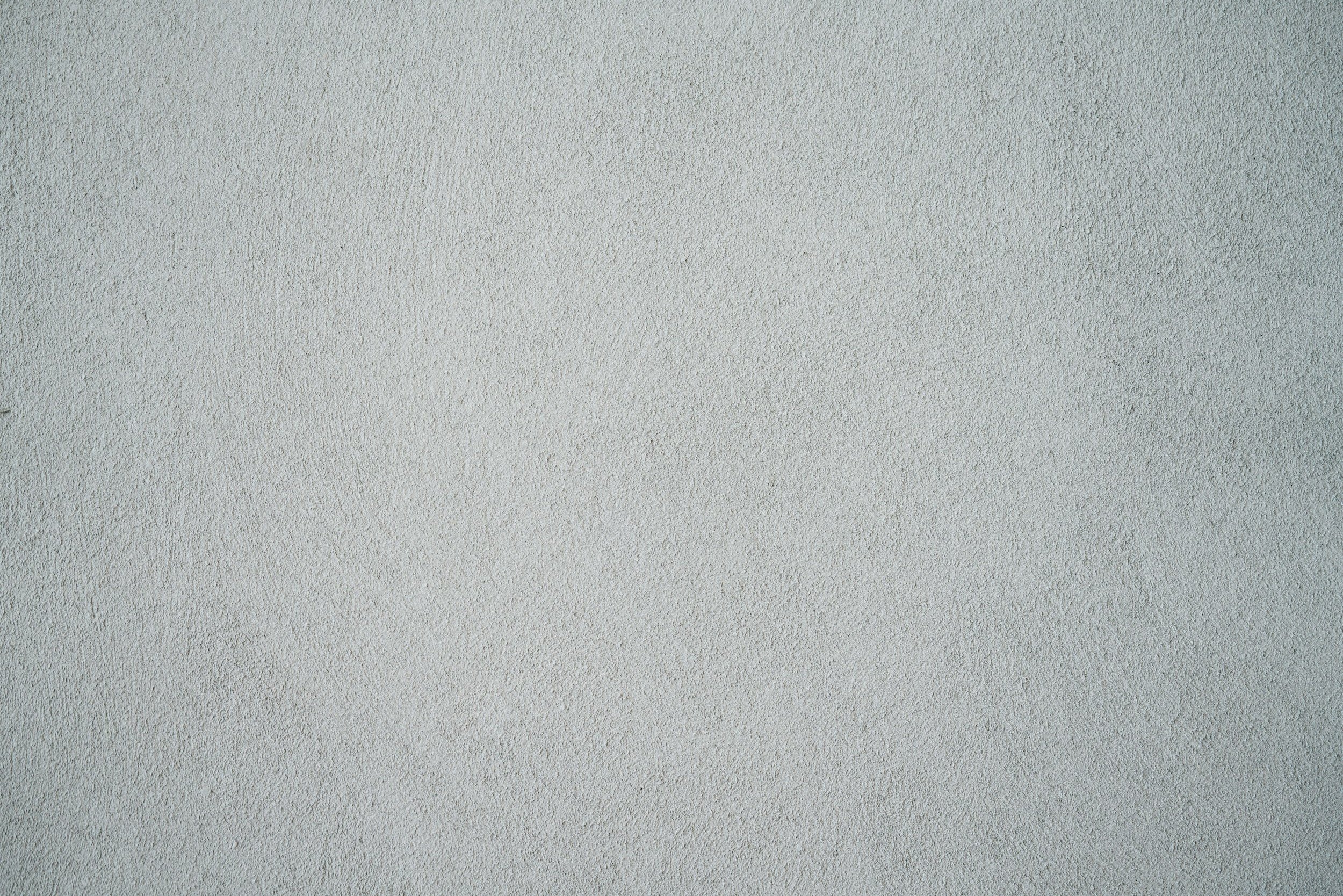
Acumatica Cloud ERP - Manufacturing Edition Module Overview
Bill of Materials
Acumatica’s Bill of Material (BOM) and Routing application connects materials, work instructions, and overhead costs to operations, facilitating time-phased material releases.
Key Features of the Bill of Materials Module
Effective/Expiration Dates: Manage BOMs with defined start and end dates to ensure materials and processes are current and accurate.
Phantom Bills of Material: Simplify the management of assembly processes by using phantom BOMs to streamline complex product structures.
Multi-Level Visual BOM: Visualize multi-level BOMs to see components and sub-assemblies, providing both an engineering and a costed view of the entire product structure.
Production Management
Take control over production costs and schedules with automation and real-time manufacturing insights using Acumatica’s Production Management Module. This module enables manufacturers to streamline and automate production planning, create production orders from bills of material and routing standards, release and schedule production orders, manage outside processes, and track materials and labor costs for work in process (WIP). With detailed cost analysis reports, inquiries, and dashboards, manufacturers gain valuable insights into their production processes, allowing them to respond flexibly to changes and maintain efficiency.
Key Features of the Production Management Module
Production Order Management: Create and manage production orders to fulfill customer demand, whether from sales orders or through the material requirements planning (MRP) application. Capture and analyze manufacturing material, labor, machine, tool, overhead, and outside process costs in real-time.
Real-Time Dashboards and Reports: Monitor production orders and gain insights into production order status and job costs through configurable dashboards, flexible Generic Inquiries, and personalized reports, such as the Production Order Labor Efficiency Report.
Adaptability and Flexibility: Maintain full lot and serial traceability, substitute operations and materials on a production order, and streamline outside processing for vendor shipments and costs. The module supports both make-to-order (MTO) and make-to-stock (MTS) manufacturing environments, helping manufacturers adapt to changing schedules and unexpected events.
Material Requirements Planning (MRP)
Acumatica's Material Requirements Planning (MRP) module ensures that materials are procured or manufactured just in time, optimizing inventory levels and aligning supply with demand. This module helps planners respond effectively to real-world changes that impact demand and production schedules through critical material reports and exception messages. It drives material requirements plans from the Master Production Schedule (MPS), identifies critical materials, and manages plans by exception to ensure smooth and efficient production operations.
Key Features of the MRP Module
Time-Phased Planning: Generate time-phased manufacturing and purchasing plans tied to forecast and customer demands, reducing inventory, improving customer service, and avoiding shortages and stock-outs.
Exception Management: Identify critical materials impacting production schedules, manage by exception to identify what needs to be purchased, transferred, or produced, and access recommendations to defer, expedite, and delete supply items.
Master Production Schedule Integration: Drive material plans from the Master Production Schedule (MPS), ensuring that MRP plans all requirements based on the MPS and treats it as pre-planned production orders, acting as the supply for other demand requirements.
Manufacturing Estimates
The Acumatica Manufacturing Estimates module allows job shops and make-to-order manufacturers to create precise and fast estimates for new items based on customer specifications or supplied engineering drawings. This module controls costs and markups for fixed and variable cost elements and integrates estimating with quotes through an embedded CRM system, ensuring a seamless and efficient estimation process.
Key Features of the Manufacturing Estimates Module
New Item Estimates: Create estimates for new items not currently in inventory, and quickly convert these estimates to inventoried finished goods and manufacturing bills of material and routings.
Integrated Sales Process: Generate sales quotes, sales orders, and production orders from approved manufacturing estimates, integrating the entire sales process for custom-manufactured products.
Flexible Estimate Creation: Create detailed or summary estimates using a bill of material structure, copy or modify existing estimates, bills of material, or production orders, and maintain multiple revisions of the same estimate while keeping a history of all changes.
Product Configurator
The Acumatica Product Configurator module offers a powerful, rules-based solution for defining attributes and formulas to create unique bills of material and routings for finished goods. This flexibility streamlines the quote-to-order and manufacturing process by allowing custom configuration of products based on features, options, and dimensions, ensuring precise cost and pricing calculations.
Key Features of the Product Configurator Module
Rules-Based Configuration: Define flexible configuration rules to calculate component quantities, costs, and customer pricing using pre-defined attributes, features, and options.
Dynamic Formulas: Create formulas for calculated quantities and costs, ensuring accurate pricing and material requirements for custom configurations.
Seamless Integration: Configure products directly for quotes, sales orders, and production orders, integrating the entire sales and manufacturing process for customized items.
Advanced Planning and Scheduling
The Advanced Planning and Scheduling (APS) module in Acumatica Manufacturing Edition empowers manufacturers to efficiently manage and monitor their shop floor schedules and work center capacities. By considering finite resource availability, this module ensures accurate delivery dates, optimizes manufacturing production, and handles constraints such as materials, production capacity, process sequences, tooling, and facility schedules.
Key Features of the Advanced Planning and Scheduling Module
Finite Capacity Scheduling: Determine how much work can be produced within a given timeframe by considering various resources and demand limitations.
Capable to Promise (CTP): Enable sales and customer service representatives to calculate realistic delivery dates based on capacity constraints, vendor lead times, and material availability.
Visual Scheduling: Visualize your production schedule with a graphical view of production order operations by work center and machine, enhancing clarity and efficiency in resource allocation.
Engineering Change Control
The Engineering Change Control (ECC) module in Acumatica ERP ensures accuracy in bill of material and routing definitions, preventing negative impacts on material planning, and cost analysis. ECC helps manufacturers maintain control of master data amidst constant change by automating the engineering change request (ECR) and change order (ECO) processes, streamlining design processes, and leveraging defined approval workflows.
Key Features of the Engineering Change Control Module
Automated Change Management: Combine multiple Engineering Change Requests into a single Engineering Change Order, and automate the change process from request to BOM update, ensuring efficient handling of modifications.
Approval Workflows: Utilize Acumatica’s Approval and Assignment Maps to route changes through defined approval processes, ensuring that changes are controlled and authorized.
Insightful Comparisons: Leverage Where-Used and Engineering Workbench comparisons to visualize changes quickly and understand their impact, enhancing decision-making and design accuracy.
Acumatica for Arena Native Connector
The Acumatica for Arena Native Connector empowers manufacturing engineers to seamlessly design new parts and modify existing ones within Arena by PTC. This module manages comprehensive engineering changes across various disciplines, including mechanical, electrical, software, packaging, and documentation, while facilitating supply chain collaboration, regulatory compliance, and quality management.
Key Features of the Acumatica for Arena Native Connector Module
Harmonized BOMs: Synchronize pre-production engineering bills of material (BOMs) and revisions from Arena to Acumatica, ensuring alignment between engineering and manufacturing BOMs.
Reduced Hand-off Time: Streamline the transition from engineering to manufacturing, reducing the time required for product release and revisions.
Advanced PLM Features: Leverage advanced product lifecycle management features to manage the entire product lifecycle, from design to manufacturing, with integrated connectivity eliminating duplicate data entry.
Manufacturing Data Collection (MDC)
Automate shop floor material and labor transactions with barcode scanning and mobile apps for real-time visibility into production processes. The Manufacturing Data Collection Module ensures detailed work-in-process (WIP) analysis through efficient data capture and automated entry.
Key Features of the Manufacturing Data Collection Module
Barcode Automation: Print barcodes on production tickets and labels to streamline material movement and labor transactions, enhancing accuracy and reducing manual entry errors.
Mobile Compatibility: Use rugged mobile devices and personal smartphones (iPhone/iOS and Android) for flexible data entry, allowing clock-in and clock-out operations directly from the shop floor.
Real-Time Data: Automate data entry for inventory updates and WIP, providing live data via role-based dashboards and actionable reports, with push notifications for immediate attention to shop floor incidents.
Warehouse Management System
The Warehouse Management Module streamlines warehouse operations through barcoding and mobile data entry, enhancing accuracy and efficiency. Automate key processes like pick, pack, ship, put-away, and physical inventory transactions, all while maintaining visibility and control with role-based dashboards for warehouse managers, receiving clerks, and shipping personnel.
Key Features of the Warehouse Management Module
Barcode Scanning: Minimize data entry errors and improve inventory transaction accuracy with efficient barcode scanning for lot and serial numbers.
Mobile Automation: Automate pick, pack, ship, put-away, and physical inventory transactions from mobile devices, reducing fulfillment cycle times and increasing productivity.
Role-Based Dashboards: Stay on top of warehouse operations with role-based dashboards, providing insights into stocking levels, costs, and activities for warehouse managers, receiving clerks, and shipping personnel.
Order Management
The Order Management Module streamlines the sales of stock products and non-stock services or digital items while optimizing sourcing activities with purchase orders and requisitions. It integrates inventory features for both purchasing and sales, providing a comprehensive solution for harmonizing supply chain activities to enhance customer and vendor satisfaction.
Key Features of the Order Management Module
Sales Order Management: Create quotes, enter orders, or synchronize orders from commerce storefronts or connected EDI applications. Implement flexible pricing and discounting strategies, and manage order fulfillment options efficiently.
Purchasing Management: Gain insights into what to buy, how much, and when with replenishment suggestions. Link sales orders with purchase orders, allocate received items to orders, and create requests for vendor quotes with bidding and configurable approval workflows.
Stock and Non-Stock Items: Manage services and digital products without Inventory Management or access advanced inventory features for sales and purchasing when integrated with the Inventory Management application.
Inventory Management
Simplify inventory processes with flexible item management, quality traceability, and robust replenishment to balance supply and demand. Optimize stocking levels to avoid rush orders and stock-outs, resulting in increased inventory turns and lower carrying costs.
Key Features of the Inventory Management Module
Flexible Locations: Manage multiple warehouses with specific inventory quantities, allocations, and costs. Define bins, use carts for picking and put-away, and set default locations for receipts, returns, and shipments to optimize warehouse efficiency.
Item Management: Streamline item creation with matrix items using attribute variables. Build kits with flexible disassembly features and set up cross-references between internal, customer, and vendor items with unit of measure conversions.
Traceability and Replenishment: Track inventory by lot or serial number with quality traceability. Automate replenishment using min/max, economic order quantities (EOQ), safety stock, seasonality, lead times, and other factors to minimize carrying costs while maximizing fill rates and inventory turns.
Financial Management
Acumatica Financial Management offers a comprehensive suite of accounting applications designed to manage both small-to-medium businesses and complex, multinational enterprises from a single platform. Integrated with project accounting and customer relationship management, it provides real-time financial insights and supports efficient business operations.
Key Features of the Financial Management Module
Comprehensive Financial Oversight: Access a complete view of financials from anywhere, on any device. Create or modify financial reports using the Analytical Report Manager, and gain real-time insights through role-based dashboards.
Automation and Efficiency: Automate critical processes with configurable workflows and scheduled bank feeds. Streamline recurring billing, expense receipt creation, and time entry with mobile applications to enhance operational efficiency.
Scalable and Integrated: Add unlimited users at no additional cost, and manage financials for multiple entities with intercompany accounting. Automate financial reporting, consolidation, payments, and cash management while leveraging AI and machine learning for advanced process automation and analysis.